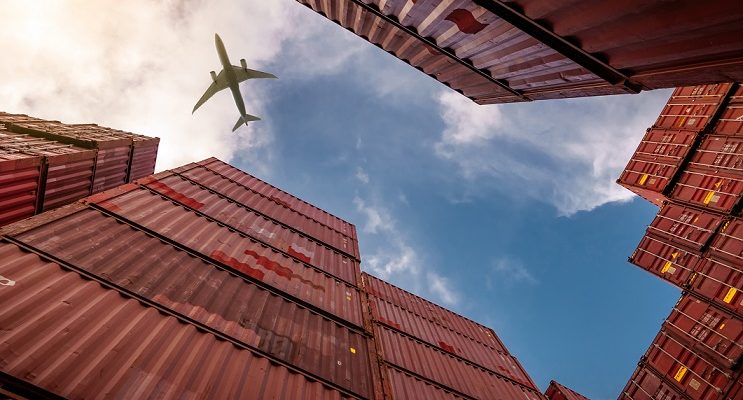
The material world of aerospace: superalloys and coatings
2020 was not the easiest year for the aerospace industry. It is said that necessity is the mother of invention, and the likely increased constraints on the aerospace industry provide an opportunity to innovate once the ‘new normal’ is normal no more. The UK Government has leant into this, recently announcing an intention to invest £90m into aerospace manufacturing.
The industry has long been geared towards improving efficiency of aircraft, and materials selection plays a significant part in this. Back in February 2020, we took a look at how composite materials were being used – in particular for reducing the weight of the airframe and engine parts. But composites aren’t the only players in town when it comes to aerospace materials.
Turbines: hotter, faster, and more efficient
Gas turbine engines are more efficient (and so use less fuel for a given journey) when they are able to operate at higher temperatures. Materials used in gas turbines therefore need to be able to operate at these high temperatures.
There’s more to think about for high-temperature applications than “Will it melt?” – creep, and creep resistance is an important factor to consider in materials selection for gas turbines. Creep is the plastic (irreversible) deformation of a material under load, which eventually results in the material breaking. Creep becomes a noticeable issue when metals are required to operate above 30% of their melting temperature, and when polymers are required to operate at high temperatures in general.
Creep resistance is improved by the use of high melting point metals, such as nickel-based superalloys. Single-crystal nickel superalloys are often used in turbine blades and have no grain boundaries. This increases their creep resistance significantly, because grain boundaries are easy diffusion paths for dislocations (which cause atoms to slide over one another and the material to deform).
Another phenomenon to consider is corrosion. Placing two different species of material together (such as steel and nickel-based alloys) could lead to corrosion of one or both of the components. At high temperatures, this effect is magnified. Thermal barrier coatings are used throughout turbines to improve corrosion and oxidation resistance, as well as reduce thermal fatigue. Thermal barrier coatings are commonly used to protect nickel-based superalloys from both melting and fatigue in turbines, and contribute to a turbine set-up where the temperature actually exceeds the melting point of the super-alloy. Selecting a coating also comes with its own considerations – adhesion, thermal expansion relative to the component, and strength matching must all be taken into account.
As might be expected with such a hot topic, there is a huge number of patents and applications directed to these superalloys and coatings suitable for use in gas turbines. Like with composites, this means a targeted approach is the most likely way to get useful protection. Even in 2012, applicants were limiting to specific alloy compositions that provided an improvement to one or more properties of the ‘standard’ superalloy (US8858873 – in this case oxidation resistance). This approach has evidence of success (US10640849B1, EP3647442B1) and provides protection both for the specific composition being used by the patent owner, and any slight variations that fall within the claimed range of compositions – so can be potentially useful in other high-temperature applications.
Alternative approaches could be to focus on the method of manufacture (US10633740B2, EP3388545B1), or distinct characteristics (US10794197B2) and applications of the superalloy or coating.
These examples show that, despite the packed field, there is room to manoeuvre if you can focus on the features that set your superalloy, coating, or component apart from what went before.
Barker Brettell has a dedicated Aerospace Sector group that can assist and advise you on how to achieve the best protection for your invention – superalloy or otherwise. To continue the conversation, please contact the author or your usual Barker Brettell patent attorney.