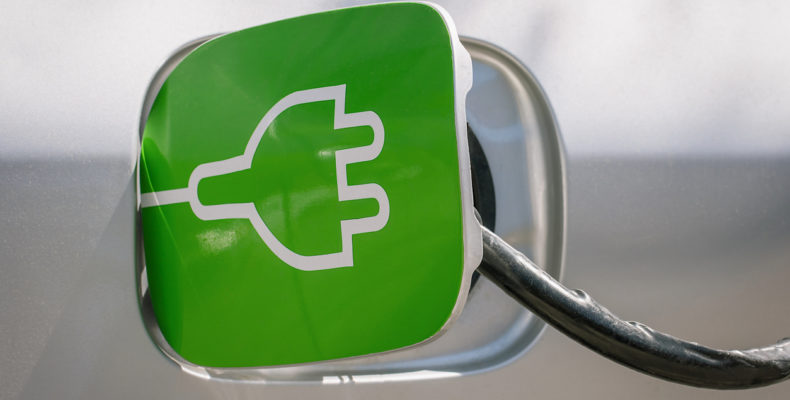
Keeping electric cars green: battery recycling innovation
Electric cars are great for eliminating at-vehicle emissions, but, even with a 10-20 year battery life-span, it will not be long before we have a large amount of ‘dead’ batteries on our hands. The materials of these spent batteries can be hazardous if not disposed of properly. Yet this presents an opportunity – many of the battery materials (especially metals) are valuable, making the recycling of end-of-life batteries potentially profitable. This also feeds into the development of a circular economy for car batteries by reducing dependence on mining more of the metals.
One key challenge is how best to separate different components of the batteries – in particular, electrode and current collector layers – so as to separate the streams of materials for recycling. In current batteries, these layers are generally bound together tightly, often with a polymeric binder.
Traditionally, methods of lithium ion battery recycling include mechanically shredding the electrodes and treating the shredded materials with a chemical etchant or a solvent capable of dissolving the binder. Other known recycling methods include pyrometallurgical and hydrometallurgical metal reclamation.
Pyrometallurgical metal reclamation uses a high-temperature furnace to reduce the component metal oxides to an alloy, generally of Co, Cu, Fe and Ni. The high temperatures involved mean that the batteries are ‘smelted’ – this process is already established commercially for consumer lithium ion batteries. At higher temperatures the polymeric binders and any other plastics decompose and burn off, and the products of the pyrometallurgical process are a metallic alloy fraction, slag and gases. The metal alloy can be separated through hydrometallurgical processes into the component metals, and the slag typically contains the metals aluminium, manganese and lithium, which can be reclaimed by further hydrometallurgical processing, or alternatively the slag can be used directly in other industries, such as cement production.
In pyrometallurgical processes, there is generally no reclamation of the electrolytes or the plastics (approximately 40–50% of the battery by weight), nor other materials such as the lithium salts. In addition to the limited number of materials reclaimed, there are also environmental drawbacks (such as the release of toxic gases and the requirement for hydrometallurgical post-processing), and high energy costs. More effective recycling could therefore provide a greater number of valuable materials, as well as improving the ‘green’ credentials of electric cars.
There is a growing number of innovative companies and research bodies working to improve battery recycling processes. Developing safe and cost-effective ways to recover battery materials for re-use has been recognised as a key factor in sustainably transforming transport. Over 120 patent applications relating to battery recycling have been published so far this year, showing that this is a hot topic.
Here in the UK, The Faraday Institution launched its ReLiB project (Recycling of electric vehicle Lithium-ion Batteries) in 2018 with over £14 million in funding, which has supported the installation of new battery testing and storage facilities at the University of Birmingham, among other projects.
Researchers working at the Universities of Birmingham and Leicester have developed a new method for separation Li-ion battery layers with support from The Faraday Institution – using targeted ultrasound. The researchers appreciated that the three-component phase boundary between the active material, binder, and current collector or metal is crucial, and that high-powered ultrasound could be used to induce cavitation near that phase boundary. The implosion of bubbles formed by cavitation induces shock waves in the material, prising apart the phase boundary mechanically, so physically separating the layers without any need of chemical reactions. The use of cavitation – rather than simply ultrasound vibrations – provides a much stronger, focused, force at the phase boundary, to tear apart the materials.
This innovation has the potential to provide a quick, clean, and continuous separation process, with automatically separated output streams, so allowing multiple different materials from the same battery to be collected and re-used.
An electrode sheet (electrode material bound to a current collector) is moved through a tank of water, and a specially-arranged ultrasound probe is used to induce cavitation in the area where electrode material, binder, and current collector material meet – the delaminated electrode material floats to the top and can easily be scooped out, leaving the clean current collector (e.g. a metal foil) behind. No high temperatures or etching acids are required. If separation of the binder from the active electrode material is wanted, a suitable solvent can be used in the tank instead of water, or the scooped-out material can be washed with a solvent later to dissolve it.
Environmental concerns – shown in both changing consumer preferences and government targets – are steering the automotive sector towards a more electrified future, and the efficient recycling of batteries is a key tool in making that future sustainable. It is also important to remember that some of the difficulties in battery recycling could be addressed by improved product design – there is scope for innovation by battery manufacturers in cell design itself, and how the cells are joined together to form battery packs and modules, as demonstrated by interest in the technology of Birmingham-based start-up Aceleron.
Barker Brettell has a large and experienced team of patent attorneys who specialise in innovation in the energy field. Please contact the author if you would like to discuss battery design and recycling in more detail, or your usual Barker Brettell attorney.