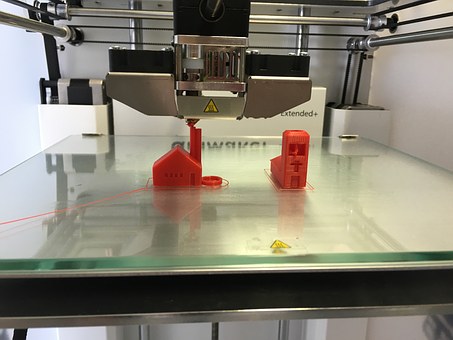
Hair-raising developments in medical materials
Tailoring the properties exhibited by a material has classically focussed on altering its chemical or compositional nature (for example, to create new alloys). At the cutting edge of medical technology, however, rapid developments in manufacturing and processing techniques are enabling existing materials to be used in new and ever more diverse applications.
Hair restoration
A team from the Columbia University Irving Medical Center has recently developed a method of growing human hair for use in hair transplants, removing the reliance on the availability of donor hairs for hair restoration surgery. By patterning collagen and human fibroblasts to form a thin gel, a human skin construct was produced. A 3D-printed device having a number of long, thin projections was then used to pattern deep, narrow wells into the skin construct. In turn, hair follicles were grown in the wells, with the skin construct able to be transplanted back into a patient’s scalp. The key development was the projections of the patterning device being 0.5 mm wide with an aspect ratio of 100:1 – a structure only made possible by recent advances in 3D printing technology.
However, the medical benefits provided by 3D printing developments aren’t just limited to improving aesthetics.
Osteochondral tissue
Articular cartilage forms the smooth outer surface at the end of bones. It can be damaged, and this damage frequently occurs as a result of sports injuries. However, osteochondral tissue naturally exhibits a gradient in its hardness depending on its distance from the bone – this can be difficult to recreate using intrinsic material properties alone. To address this issue, researchers at Rice University have developed a method of 3D printing scaffolds on which bone and osteochondral tissues can be grown. By using different porosity levels and different pore sizes when 3D printing the scaffolds, bespoke implants mimicking the gradient in hardness naturally exhibited by osteochondral tissue can be produced.
Collagen braces
Similarly, customisable joint supports or braces based on the biological structure of collagen have been developed by engineers at MIT. Collagen has a microscopic hierarchical structure formed in part by intertwined strands which contribute to its outstanding and variable mechanical properties. Using 3D printing of extruded thermoplastics, flexible meshes having a similar structure to collagen can be produced. The stiffness of different regions of the mesh can be tailored by incorporating slack and modulating bonding between filaments, allowing the mesh mechanics to match non-linear responses of body tissues such as muscles and tendons. Such meshes can be used as braces to support a joint in one direction whilst allowing unconstrained movement in another direction. As a proof of concept, an ankle brace preventing inward rotation whilst allowing normal walking movements was produced preventing repeat injury and aiding recovery without impacting on daily activities
The above examples illustrate that as materials engineering and manufacturing continues to develop, the behaviour of materials (mechanical or otherwise) is increasingly defined by extrinsic properties like structure and production method as by intrinsic material properties. For such inventions, it is therefore essential to consider what the most suitable patent protection might be – the material itself, the method of production, or both.
Barker Brettell has a dedicated medical sector group. If you would like to discuss options for protecting your invention, please get in touch with one of the team or contact your usual attorney