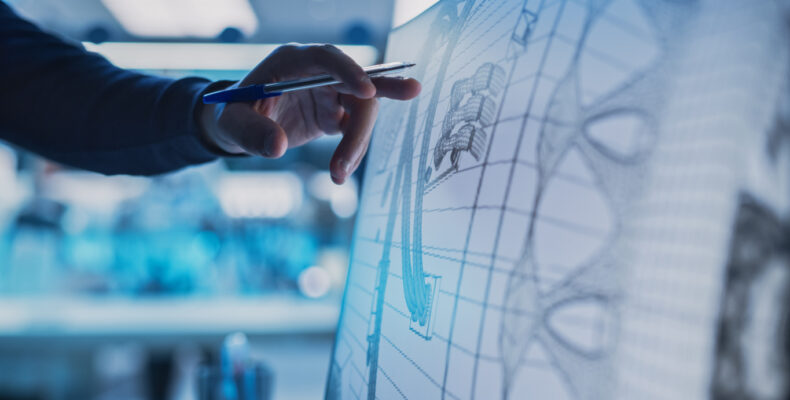
Winging it
Innovation in aircraft design
In general, the design of production aircraft has not radically changed since the mid-twentieth century. For decades, large aeroplanes have adopted a ‘tube and wing’ architecture, epitomised by the likes of the Boeing 747 and Airbus 830 families. Similarly, propulsion on fixed wing production aircraft has not evolved significantly since the invention of the gas turbine engine. And rotorcraft have remained substantially unchanged since the first large-scale mass-produced helicopter, the Sikorsky R-4, was first developed in the 1940s.
That being said, the aerospace industry has never been short of radical experimental aircraft, such as the Vought V-173 “Flying Pancake”, the Grumman X-29 with its forward-swept wings, and MIT’s ionic wind-powered prototype. This tradition of innovation continues to push the development of aerospace design and technology.
Today, the key driver behind innovation in the aerospace industry is sustainability; increasing efficiency and reducing emissions. In a previous article, we explored how alternative energy sources are being investigated in an effort to decarbonise the aerospace industry. Here we will look at how innovation within two key aircraft design areas – aerodynamics and propulsion – seek to address the issue of sustainability. Specifically, we will look at innovations in wing design, and the introduction of distributed electric propulsion.
Wing design
A key contributor to aircraft emissions is aerodynamic efficiency, which can be defined by the lift-to-drag ratio of an aircraft. Aerodynamic efficiency can therefore be increased by reducing drag. Perhaps the greatest opportunity for reducing drag is through wing design. As such, wing designs which seek to maximise aerodynamic efficiency have emerged over the years.
One example of such a design is a canard wing configuration. An example canard wing configuration utilises small wings arranged forward on an aircraft – the canard wings – in combination with the main wings of the aircraft, which are arranged at the rear of the aircraft. Whilst the effects of canard wing arrangements are complex and varied, they can be employed to reduce the overall drag on an aircraft. This, in turn, creates a trade-off with aircraft stability. But as wing designs improve, we may well see the wider use of canard wings on production aircraft.
An example of a somewhat radical wing design which seeks to improve aerodynamic efficiency is the blended wing. As the name suggests, a blended wing design blends the fuselage of an aircraft into the wings, such that entire body of the aircraft is designed to generate lift. A blended wing design is currently being developed by US company JetZero (not to be confused with the UK government’s strategy for achieving net zero aviation by 2050). JetZero claim that its design can cut fuel emissions in half compared to a typical commercial airliner.
A final wing design example is the use of strut or truss-braced wings. In this configuration, the wings are structurally supported by struts or trusses extending between the wings and the aircraft fuselage. This additional structural support allows for the use of longer and more slender wings, which produce less drag in flight. An example of an aircraft utilising this wing configuration is the Boeing X-66, a demonstrator of which is scheduled to fly in 2028.
Distributed electric propulsion
Another relatively recent innovation in aircraft design is distributed electric propulsion (DEP). DEP utilises an array of, typically, three or more independently controlled electric propulsion units. Some DEP systems utilise a large number of propulsion units, sometimes in double figures. The propulsion units are typically arranged across the span of the wings of an aircraft. DEP can improve aircraft efficiency through a number of mechanisms, such as aero-propulsive coupling, i.e., the interaction between aerodynamic and propulsive forces to reduce drag and increase lift. DEP can also provide improvements in safety, through redundancy of the propulsion units, and in noise reduction, making aircraft utilising DEP particularly suitable for very short haul and urban transport. Examples of these types of aircraft include the Lilium jet and the Airbus CityAirbus NextGen. Examples of larger aircraft utilising DEP include the Airbus E-Thrust and the NASA N3-X.
Combined innovation: aerodynamics and propulsion
The aircraft of the future will likely combine innovations in both aerodynamics and propulsion. This is demonstrated in the aforementioned aircraft. Another example aircraft is the Airbus Racer, which saw its first flight this year. The Airbus Racer appears at first glance to be a conventional helicopter. However, unlike a conventional helicopter, the Racer utilises an innovative box-wing design to improve aerodynamic efficiency and generate lift in addition to the main rotor and two pusher propellers to generate thrust. In combination, this provides efficiency gains resulting in a claimed 20% fuel reduction compared to conventional helicopters of the same maximum take-off weight category.
Summary
It is difficult to image aircraft looking significantly different over the coming decades. However, in the pursuit of sustainability, we may well see aspects of designs we once considered to be radical start to creep into production aircraft. In any event, as history and contemporary developments have shown, the potential for innovation within aircraft design is vast.
Barker Brettell has a dedicated aerospace group that can help you commercialise your innovations. Our patent attorneys possess knowledge and experience across the entire range of technologies utilised within aerospace, from computer-implemented inventions and electronics to materials science and mechanical engineering. If you would like to discuss this article in more detail, please contact the author or your usual Barker Brettell attorney.